Keihin CR Special Smoothbore Carburetor Troubleshooting Guide Manual HERE. Keihin CVK32 Carburetor Maintenance Service Instruction Tuning Manual HERE. Mikuni HS40 HS 40 Carburetor Illustrated Parts List Diagram and Tuning Manual HERE.
- Keihin Carburetor Schematics
- Keihin Ks2 Carburetor Manual Pdf
- Keihin Carburetors Kohler
- How To Identify Keihin Carburetors
previous page | pages 12345678910ALL | next page |
Typical JDJetting Kit with Custom Machined Needles | Carburetor Throttle Circuit Range Effects | Carburetor Tuning Range Chart | Keihin Needle Chart with Small Needle Tip Notation |
Suzuki DRZ400S BSR Carburetor | FCR-MX Carburetor Parts | Eploded View 1 | Eploded View 2 |
Carburetor Clamps and Fittings | FCR1 Single Carburetor Parts | Accelerator Pump Diaphragm Spacer in Jet Kit JDK015, JDK013, and JDK002 | Needle Clip Positions for FCR carburetor needles |
FCR-MX Float Level Setting | Float Level PWK Short Body | PWK Air Striker Float Level Setting- Yamaha & KTM, 2 screw cap | Air Striker Float Level Setting- Screw Cap Version |
FCR1 Float Level Setting | Vacuum Plate Seal Orientation | Vacuum Plate Seal Orientation 4 | Vacuum Plate Seal Orientation 2 |
Vacuum Plate Seal Orientation 5 | 1990 Keihin PWK Float Height and FUEL Level | FUEL Level | TPS Resistance Check #1 |
TPS Resistance Check #2 | 2011 YZ450F TPS Setting | Jets and Needle Clip Positions | Pilot screw (Fuel Screw) |
Accelerator Pump | Accelerator Pump Linkages 1 | Accelerator Pump Linkages 2 | Carburetor Bottom with Pilot Screw, Spring, Washer, and O-ring |
Carburetor Slide and Plate (Square End is Down on Plate) | Carburetor Cables, Hoses, and Clamps | Setting the Pump Timing Start point | FCR Single Taper Needles |
PWK/PJ Single Taper Needles | Keihin PWK PJ Single Taper Needles | FCR Needles list.gif | Yamaha YZ426 Needle Info.jpg |
Power Bowl with Adjustable Pump | FCR Carb disassembly for clearing pump nozzle | FCR Carb disassembly for clearing pump nozzle | FCR Carb disassembly for clearing pump nozzle |
FCR Carb disassembly for clearing pump nozzle | FCR Carb disassembled | Two small passages flow fuel from the pilot jet, however, only the lower opening is metered by the fuel screw | IMG_3275.JPG |
IMG_3267.JPG | IMG_3270.JPG | IMG_3278.JPG | Accel Pump Nozzle and Pilot Jet Passages.jpg |
Keihin FCR Gaskets at Middle of Carburetor.jpg | FCR Mid-Body Gasket Set #JDKH17 | Gaskets at Middle of Carburetor - JDJetting part JDKH33 | Mid Body Gasket with Bubble Shape Included- JDKH33 |
Standard Nozzle with Single Passage | Dual Spray nozzle #JDKH27 | FCR Carb Disassembly for Pump Nozzle Access and Dual Spray Installation | Dual Spray Nozzle Installed, #JDKH27 |
Standard Accelerator Pump Nozzle Compared to Dual Spray Nozzle from #JDKH27 | Standard Accelerator Pump Nozzle | Dual Spray Accelerator Pump Nozzle from #JDKH27 | Mid Body All Gaskets FCR-MX, Upper gaskets are in #JDKH17, JDKH33, and Dual Spray Nozzle #JDKH27 |
Mid Body Gasket JDKH17 Cut to Fit FCR Carb with Removeable Flange | JDKH17 vs JDKH33 -Use JDKH17 to Cut and Fit | JDKH17 vs JDKH33 -Use JDKH17 to Cut and Fit | 3M Scotch Weld 847 KTM Recommended Product to Seal the Mid-Body Gasket |
3M_Adhesive_847 | Keihin FCR Mid-Body Gasket Set #JDKH17 | FCR Mid-Body Gasket Set #JDKH17 (1 of the 2 large gaskets included is shown) | FCR Mid-Body Gasket Set #JDKH17 (1 of the 2 large gaskets included is shown) |
Gasket and Rebuild Kit #JDKH20 | Slide Plate #JDKH22 and Seal #JDKH19 | FCR Mid-Body Gasket Set #JDKH17 | Dual Spray Accelerator Pump Kit #JDKH27 |
NOTE- THESE ARE PICTURED UPSIDE-DOWN: Pump Diaphrams- Standard #JDKH18 (on left), and Honda Diaphragm #JDKH04 (on right) | Quickshot 3 Adjustable Pump Cover- Part #JDAP05 | Replacement Float Needle and Seat for FCR-MX Select Models 2000-2005 | The Float Needle Seat is Removable and Can Be Replaced with This Version FCR-MX |
Quickshot 3 Adjustable Pump Cover- Part #JDAP05 | FCR Carb disassembly for clearing pump nozzle | Cleaning Pump Nozzle- Location to Spray Carb Cleaner | KTM Slide with Notch and JDJetting Modified Replacement Slide |
KTM Slide with Notch and JDJetting Modified Replacement Slide | KTM Slide with Notch and JDJetting Modified Replacement Slide | KTM Slide with Notch and JDJetting Modified Replacement Slide | KTM Slide with Notch |
JDJetting Modified Replacement Slide for KTM | KTM Slide with Notch and JDJetting Modified Replacement Slide | JDJetting Modified Replacement Slide for KTM | Adjustable Pump Cover No Longer Available |
CO Content vs AirFuel Mixture | Needle_change_of_fuel_with_clip | Needle_percent_change_of_fuel_with_clip | Needle_change_of_fuel_with_clip_NOZI |
Needle_percent_change_of_fuel_with_clip_NOZI | Needle_change_of_fuel_with_clip_N8RH | N8RH VS N3EH 2 and 3 | Needle_percent_change_of_fuel_with_clip_N8RH |
Keihin Needle Designs N3CA to N3CM | Needle NOZH vs DDJ DEL CEL CCK | Needle NOZH vs DDJ DEL CEL CCK | Keihin PWK Needles NOZE NOZF NOZG NOZH |
Needle_and_pilot_jet_Change | Needle_and_pilot_jet_Change Percent | NAFG_vs_N8RG vs Single Taper R1471E | NAFG_vs_N8RG vs Single Taper R1471E |
NAFG_vs_N8RG vs Single Taper R1371E | NAFG_vs_N8RG vs Single Taper R1371E | Textbook Richening with needle clip vs taper and main jet | PWK 38mm vs 36mm Engine Side |
PWK 38mm vs 36mm Air Filter Side | Jetting Guide Examples of Double and Triple Taper Needles Profiles | Jetting Guide Examples of Double and Triple Taper Needles | N3CW and Richer Needles by Half Clip |
N3CW and Richer Needles by Half Clip Percent Change in Fuel |
- Keihin CVK32 Disassembly. Tools Needed: Long shank #3 Philips screwdriver, 8mm wrench, 3mm Allen wrench, Thin long shank flat blade screwdriver, toothpick or similar implement and optional items; silicone grease and Pin gage set.
- 1980 Indian AMI50 Indian AMI50 carburetor Keihin PA M0A-A. Late PC50: The carburetor changed from “donut” float to a swinging float, and a NC50-type float bowl and gasket. The 1973-77 PC50K1 and 1973-78 PF50 engine and carb are the same as the Taiwan remake engine and Keihin carburetor used on the 1978-83 Indian moped.
previous page | pages 12345678910ALL | next page |
Keihin FCR tuning manual Version 3.3 By Patrick Burns |
Many thanks to Marc Salvisberg, founder of Factory Pro Tuning, for teaching me the finer points of using dynamometers and tuning carburetor equipped engines. I'm sure he still disagrees with some of what's here (my dislike of changing float level, and even suggesting that one use a lambda sensor, for examples...), but this version of my FCR tuning manual is a lot better than the ones I wrote before I did my stint as a technician at Factory.
Thank you, Marc.
After attending some AMA road races over the last few years as a dynamometer operator for Factory Pro Tuning and mechanic for Ricci Motorsports, and having the opportunity to talk with lots of racers, I've learned to my absolute horror and amazement that you people are actually *using* the information on this page to tune your race bikes. God help you all.
Someone asked me for info on using a Dynojet inertial dyno to tune a bike equipped with FCRs. Since I'm all too aware of the fact that most people don't have access to a proper brake dynamometer and an exhaust gas analyzer, I put together an answer.
Before you do anything, MAKE SURE THE CARBS ARE CLEAN. Tear them completely apart (don't forget to remove the idle mixture screws), blast everything with carb cleaner, and blow out all passages and jets with compressed air. If you neglect this critical step, don't be surprised when, after fourteen jet changes, you find that a shred of fuel line or bits of rust from the gas tank (yes, even on YOUR bike, even with a fuel filter) had gotten lodged in some passage or another, causing the 'jetting' problem you were trying to solve.
If you're running a ram-air setup, and the carbs don't sit inside the airbox, you'd better route the float bowl vents to the inside of the airbox or you'll never in a million years get the thing working properly. If the ram-air works at all, as soon as the bike gets rolling along faster than a walking pace the mixture will go dead lean.
If you're running a ram-air setup, and using gravity feed rather than a pump to move the fuel from the tank to the carbs, you'd better route the fuel tank vent to the inside of the airbox or you'll wonder why it keeps sputtering at the end of long straights. 160 mph worth of air pressure in the float bowls and only ambient pressure in the tank will seriously slow down or even stop the fuel coming in from the tank, and the float bowls will run dry. You need to put airbox pressure into the tank to keep the fuel flow constant at various speeds.
And I'm not kidding about the float valve seat sizes. Scroll down to the bottom of the page to get the scoop. I didn't come up with the chart. It's straight from Keihin.
Keep in mind that you will spend much less time tuning the carburetion in following order:
1. Main fuel jet and main air jet (must be selected first since they feed the emulsion tube, which feeds the needle jet and jet needle).
2. Needle: a. root diameter b. taper c. clip position (which includes the L1 measurement)
3. Slow fuel and air jets.
4. Fuel screw
5. Accelerator pump (It helps to leave this disconnected during dyno testing so as not to create a momentary artificially rich condition which may lead to misleading exhaust gas analyzer readings. However, it's surprisingly time consuming to remove or install the pump connecting rod. If I had all the time in the world and were doing development work, I'd disconnect it. If I were at all in a rush, I'd leave it connected and just hold the test point a little longer to let the EGA get a solid reading.)
You may find that if you change the taper of the needle a great amount, you may have to go back and reselect the main fuel and air jets since the tip of the needle can affect the full throttle mixture.
Synchronizing:
I've had pretty good luck synchronizing the carbs off the bike. Using the shank of a very small drill bit, adjust the idle speed screw until you can barely fit the base of the drill bit under one of the slides as you would a feeler gauge. You may have to remove the idle speed screw from the carbs and temporarily remove its locking spring to be able to thread the screw in far enough to slide a drill bit in unless you have some pretty small bits. Do this from the engine side of the slide as opposed to the intake side, and make sure the carbs are oriented such that the slides are moving vertically, so their weight takes up any slack in the throttle linkage. Remove the top of the carbs as you would to access the needles. On the throttle shaft in each carb there is an arm which controls slide movement. It is secured by a screw and nut. The nut is used for adjustments, the screw is to lock the adjusting nut in position. Loosen the lock screw of the slide you are trying to adjust, turn the adjusting nut to set the slide so the drill bit just scrapes under, and tighten the lock screw. Repeat for each slide. Be prepared to spend about five times as long as you think it should take, going back and forth between slides to get everything just right. Replace idle speed screw locking spring. Because the carbs must be disassembled to access the adjusting mechanisms, I recommend using the above procedure. You could use manometers to synchronize the carbs as you would a set of CVs, but you'd have to start and warm the bike, check vacuum levels, shut the bike off, disassemble the carbs, adjust, reassemble, restart the bike, and recheck vacuum levels. You may very well kill the battery (or your bump start helpers) before you finished synching the carbs this way. It has been my, and others', experience that the lock screws tend to work loose with time no matter how surely you tighten them. To remedy this, after the slides are synchronized, clean the adjusters with brake or contact cleaner, blow them dry, and put a drop of silicone over their tops. You can also use Loctite 290, but it tends to make future adjustments a bit difficult. Once the bike is up and running, if manometers show that the synchronization is off by a considerable amount at idle speed, but even out as the throttle is opened, it's entirely possible that the cylinders want different idle mixtures. This is not at all uncommon, especially on V-twin engines where the intake tracts are dissimilar such as Ducati 2 valve 750s and 900s. But you'd better go and check your valve clearances first to make sure a valve isn't hanging open. If the vacuum levels are off and you're working on a V engine of some sort, make sure you didn't botch up the cam timing on one bank.
Fuel screw:
With the carbs synched, the engine warmed up to operating temperature, and the idle speed set, adjust the fuel screws so that when you rev the bike in neutral and release the throttle, the revs quickly drop to exactly idle speed again. If, when you release the throttle, the revs hang up a few hundred rpm above idle speed, then drop to idle, the idle mixture is probably a bit too lean. Turn the fuel screws out. Use a minimum of half turn increments until you know you've just about nailed it. You'll drive yourself up the wall trying to tune the thing in eighth or quarter turn increments if you're a mile off. In extremely lean cases the idle will hunt between the proper speed and something above it. If, when you release the throttle, the revs drop below idle speed then pick up, the idle mixture is probably a little bit too rich. Turn the fuel screws in. In extremely rich cases the engine will die after revving the bike and releasing the throttle, unless you've turned the idle speed screw way in, in which case it may act like the idle mixture is a little bit too lean. In slightly rich cases, the engine will respond well to throttle blips when cold, but will die or dip slightly below idle speed when hot. While having an exhaust gas analyzer is almost mandatory during tuning of main and needle circuits, do not rely totally on them to set idle mixture. Use an accurate tachometer (like your ear) and adjust the fuel screws to find the highest vacuum for each cylinder or highest idle speed, which will often be the same setting.
Slow fuel jet:
After setting the fuel screws, if you end up having to turn them in closer than 1 turn out from bottomed, select smaller slow jets. If you end up with the fuel screws turned out further than 2 turns from bottomed, select larger slow jets. Go back and repeat the fuel screw adjustment procedure. You have the correct slow jets when your engine passes the fuel screw adjustment procedure (settles to a steady idle after throttle blip) with a fuel screw setting between one and two turns out from lightly bottomed. A good way to see if the slow fuel jet is too large is to slowly turn the fuel screw closed and see if the bike still idles. If you get the fuel screw down to something like half a turn out, or closed, and that cylinder is still firing, the slow fuel jet is probably too big.
Slow air jet:
With the correct slow fuel jets installed and the fuel screws adjusted as above, when you are operating the engine at higher revs and closed to 1/10th throttle (say, while transitioning from trailing to neutral throttle or running with no load at some mid rpm), if the mixture is too rich, use a larger slow air jet. If the mixture is too lean, use a smaller slow air jet. It is rather easy to confuse this circuit with the needle’s root diameter since they overlap quite a bit. If the needle’s root diameter is very far from perfect, you will be trying to make up for problems created by that instead of dialing in the slow speed circuit. Conversely, if the slow air jet is a mile out, you’ll have a hard job of selecting a needle root diameter. To help resolve problems with this, be conscious of the fact that the slow air jet will tend to have a more pronounced effect at lesser throttle openings, and the needle's root diameter, very slightly greater.
I should point out here how the air jets and fuel jets interact. I can do this most easily with a little graph.
This graph is 100% a figment of my fevered imagination, and is only to be used as a general guide, not an absolute definitive end all be all word of truth. That said..
1. air jet way too small
2. air jet a little bit too small
3. air jet just right
4. air jet a little bit too big
5. air jet way too big
So basically what happens is if you have the mixture right at low rpm, and it's too rich at high rpm, the air jet is too small and you need a bigger one. Or if you have it just right at high rpm and it's too lean at low rpm, you have an air jet that's too small and you need a bigger one. Or if you have the mixture just right at low rpm and it's too lean at high rpm, the air jet is too big and you need a smaller one. Do I really need to type the fourth combination? When you put in a bigger air jet, it leans things out everywhere, but more at higher engine speeds. And when you put in a smaller air jet, it richens things up everywhere, but more at higher engine speeds. Then when you get the right air jet, it might be too rich or too lean everywhere, so now you have to go and put in a smaller or bigger fuel jet to fix things up again. So you control the shape of the graph with the air jet, and move it up and down with the fuel jet. The same thing is supposed to apply when working with the main air jet and main fuel jet, but it doesn't on FCRs, for reasons which I'll get into further down. But it's supposed to, damn it.
Slow air screw:
Some FCRs are equipped with a slow speed air screw in place of the slow air jet. They rock. Buy some, from Sudco, because they rock. You need the screw plus a little locking spring. The part numbers are 012-230 for the screw, and 021-235 for the spring. It'll probably cost about $60 after shipping to get four of each (um, I'm assuming you're tuning a four cylinder there). Yeah, I know that's a lot of money for four jets. But look at it like this, the jet and spring together cost something like $12. One slow air jet costs something like $4.50. If you think for one second that you're going to get the right jet size on the first try, you've obviously never done this before. If you think you're going to get it on the second try, you're Merlyn Plumlee (Is Merlyn not the coolest name for a mechanic or what?). So just buy the adjustable jet and be done with it. Aside from not having to buy a bunch of different jets, it also allows much faster changes in calibration as you need only to turn a screw as opposed to changing a jet, and you can do it with the engine running in many installations, so you can _listen_ for the change in mixture. Some air filter adapters have a 4mm passage leading to the slow air jet, some a 6mm passage. If your carbs have slow air screws and the 4mm adapters, drill the adapters' slow air passage to 6mm. This will allow you to access the air screw with a screwdriver big enough to actually turn it, but will leave a hole small enough that the jet can't fall out and get sucked into the engine if it for some oddball reason works loose (that's probably never happened in the history of the world, but it makes me feel better knowing it can't). The following number of turns out are shown with the slow air jet size they are approximately equal to. Note that the change in jet number is not linear with the number of turns out. The screw adjusters are much more sensitive at lesser openings since the screw is still moving linearly at a constant distance per turn, but the flow area is changing more or less as a function of distance open, so half a turn out is two times as rich as one turn out, but one and a half turns out is only fifty percent leaner than one turn out. Or something like that. And don't e-mail me to say look dude half a turn out is a 65 and one is a 100 and one and a half is a 125, go and find the area of the aperture of each one of those jets first then hit yourself over the head with the calculator. Like this even matters...
Number of turns out | Approximately equal |
1/4 | 45 |
3/8 | 55 |
1/2 | 65 |
5/8 | 75 |
3/4 | 85 |
7/8 | 95 |
1 | 100 |
1 1/8 | 110 |
1 1/4 | 120 |
1 1/2 | 125 |
1 3/4 | 130 |
2 | 135 |
2 1/4 | 140 |
2 1/2 | 145 |
2 3/4 | 150 |
3 | 155 |
Main fuel jet:
The proper main fuel jet will give best full throttle performance, but also affects mixture as far down as 1/8 throttle. I know you don't believe this second part, because I didn't believe it until I saw it happen while tuning an extensively instrumented test engine. Suspend your beliefs about the main fuel jet only affecting mixture when the slide is all the way up & the needle is all the way out of the needle jet and think for a minute. The main fuel and air jets feed the emulsion tube which feeds the needle jet and jet needle. When a more fuel rich emulsion is bled past the same restriction (needle jet area minus jet needle area), the engine gets more fuel. You must select the full throttle jetting first. If you go and find a needle that works with the wrong main jets, it won't work with the right ones, and you'll have to go through the needle selection process all over again when the main jets are correct. Trust me.
Main air jet:
If you find that the engine runs perfectly at WOT near the torque peak, but becomes lean toward redline, select smaller main air jets. Conversely, if the engine runs perfectly near the torque peak but richens toward redline, select larger main air jets. Changes in air jets may require changing the main fuel jet. Say you have good performance at engine speeds leading to the torque peak under wide open throttle with a 150 main fuel jet and 200 main air jet. Should you need to richen the mixture at full revs and full throttle and select a 180 main air jet, you may need to go down to a 145 or 140 main fuel jet to keep the lower rpm mixture the same as with the 150/200 combination. Generally (there are always exceptions), once the main air jets are properly selected for the intended application, they need not be changed again unless you change the intake restriction (modify the airbox or use different filter) or change engine or exhaust specification. Varying atmospheric conditions can usually be dealt with by fuel jet, fuel screw, and needle changes.
The part that really sucks about FCR carburetors is that they come with primary type emulsion tubes as opposed to the bleed type emulsion tubes every other four stroke carb in the whole universe ever used. What this means, essentially, is that the above paragraph doesn't actually have any connection to reality. It has been my experience that if you for whatever reason have something like a 200 main air jet in the carbs, and the mixture goes lean at high rpm, and you manage to get the mixture sorted out by putting in different (smaller) main air jets and main fuel jets, then the carbon monoxide numbers might be really pretty and even from mid rpm through redline, BUT THE ENGINE ISN'T MAKING AS MUCH POWER AS IT DID WITH THE BIG MAIN AIR JETS. I think this has something to do with a bigger air jet allowing the fuel coming up through the needle jet to get emulsified more before going up into the venturi, therefore allowing better atomization, and more complete burning of the fuel supplied into the cylinder, since lots of little bitty fuel droplets have more surface area per unit of volume and burn more completely, as opposed to a few big fuel droplets having less surface area per unit volume and not only burning less completely, but because they burn less completely you need to have more of them to burn the oxygen available, which means the CO and hydrocarbon numbers go up because lots of unburned fuel is hanging around throughout the combustion process, soaking up heat and getting pumped out the exhaust port. Or something.
When using a carbon monoxide meter to track exhaust gas readings, do not fall into the trap of aiming for the same CO reading at every rpm. It is quite rare for an engine to make best power at every rpm with the same CO reading. You must determine what the engine wants at each rpm, then tailor the fuel curve accordingly.
Okay, here's a good place to put the CO and O2 graph, so you know why CO is a good indicator of rich or lean conditions in gasoline burning engines being tuned for maximum power.
So the little red box is where you're aiming. It has been my experience that best power is usually had with a CO reading somewhere between 2% and 6%. That'll give you an air fuel ratio somewhere in the neighborhood of 12:1 to maybe 13.5:1. These numbers are not absolutes, don't call the SAE on me here. I don't even really know for sure that the CO and O2 graphs cross at 14.7:1, but I put it there because what the hell good is an air fuel ratio graph without having 14.7:1 on there somewhere? I think it's a tradition or something. But the deal is, if you look at the graphs, the CO graph is relatively steep compared to the O2 graph in this range of air fuel ratios, so for a small change in air fuel ratio, there's a relatively large change in CO reading, which is good, because then you have a clue what just happened when you changed jets. If you try to use O2 as an indicator in this range, what you end up with is a small change in O2 value for a large change in air fuel ratio, so you need super duper accurate equipment which is hideously expensive, so bike tuners don't have it, so you can't use it anyway, never mind that it's dumb in the first place.
You won't need a CO reading to tell you when it's above about 10% or below about 1%, because you'll be able to hear the engine misfiring. But it's still nice to know which way you need to go, because it's not always immediately obvious. And one thing about using CO as an indicator is that if you get anywhere on the low side of about 1%, you're super duper lean. 0.5% is way way leaner than 1%, and 0.2% is way way way way way leaner than 0.5%. And if you look at the graph of CO above, you'll see why that's true. So what I'm saying is if you see 0.5%, don't even bother making some little change like one jet size or half a turn on a mixture screw or air jet. You need to make a big change in the rich direction.
Reality check. Nobody likely to be reading this page can afford a four gas EGA. So you can't use CO as an indicator. You need something to go on, because reading plugs will drive you craaaaazy. Do not do not do not do not buy an EGT setup. Using exhaust gas temps to determine air fuel mixture is so much more trouble than you can possible imagine. It's worse than reading plugs, because you think you've got good info, but it's all wrong, except for when it's right, only you won't know when that is. So. Hook up a Bosch four wire lambda sensor, generic one size fits all style, that you can get for like $40 at any auto parts store. Do what you have to, to mount it in the exhaust collector. Yamaha had this really neat setup on Scott Russell's YZF750 at Daytona a billion years ago with a wide range lambda sensor (that'd be the $600 version) mounted in the mid pipe, between the header and muffler, so they could gather data during practice, then take it out and mount a regular, unmodified mid pipe for the race. That might be a nice place to mount yours. So... you want the four wire sensor because it has heaters in it, which bring the sensor up to temp a lot faster, and they have to be hot to work. And it's nice to have the sensor wire plus a real ground wire back to the sensor instead of how a three wire sensor makes you ground back through the exhaust, engine, frame, all that nonsense. You can read the voltage with a high impedence digital volt meter, or you can buy a really spiffy gauge from Nordskog Performance that shows you the true voltage signal coming from the gauge. They and K&N also sell gauges that supposedly tell you the air fuel ratio. They don't work, exactly. That's just not how the sensors work, so the gauges can't possibly give you a true value for air fuel ratio. I think you're better off just getting the pure voltage signal, and interpreting it yourself, than relying on a gauge that's telling you a fib. If you buy a gauge from Nordskog, you might as well buy a sensor from them too. They get $60 for a four wire NGK/NTK lamda sensor, but if you're busy it's probably worth it not to have to make a trip to the auto parts store and sort through all the $150 gauges to find the $40 one. I'm not going to go too deep into how lambda sensors work, but they're super sensitive around stoiciometric, and less so once you get away from there. Google on do it yourself lambda sensor stuff and I'm sure you'll find the relevant info. There's probably reams of info on the DIY EFI site. Here's a rough graph of voltage versus lambda that I stole from someone so long ago I can't remember who it was to give them credit:
The long and the short of it is you'll be aiming for a voltage reading somewhere between about 0.90 and 0.70 volt for best performance. Higher voltage is richer, lower voltage is leaner. Stoiciometric is right around 0.50 volt. But it's not linear. 0.60 volt is richer than 0.40 volt. But 0.80 volt is a lot richer (but probably still a tiny bit lean of best full throttle mixture). And 0.95 volt is total misfiring black smoke out the exhaust and all that. Anyway, enough of that. Lambda sensors are useful. They are not as good as a CO reading, but they're a whole bunch cheaper than an EGA, and they react FAST, like fractions of a second. So it's good for seeing transient stuff.

Sorry, Marc! :)
Needle code:
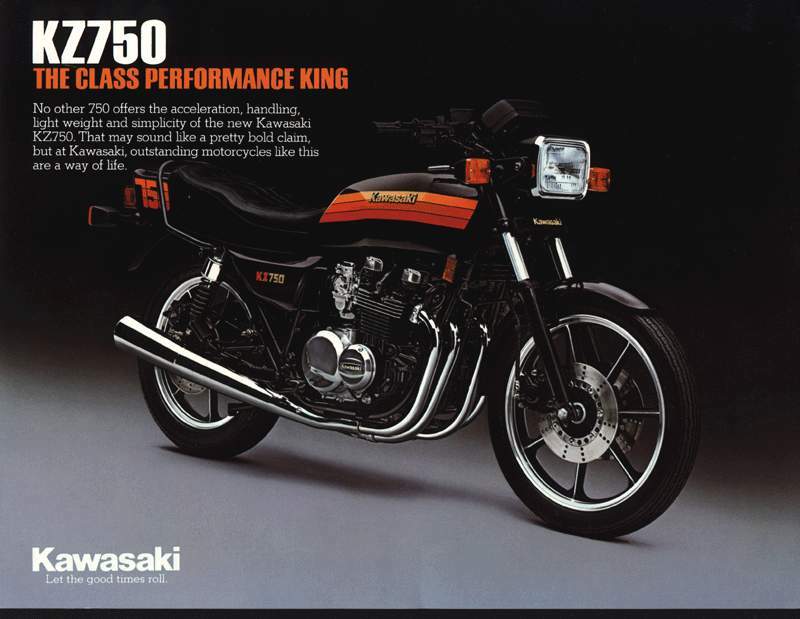
1st letter indicates taper. Letters toward the beginning of the alphabet are leaner (more gradual taper), letters toward the end of the alphabet are richer (more drastic taper).
2nd letter indicates the L1 measurement. This is the distance from the top adjustment clip to a portion of the needle where the diameter is 2.515 millimeters. Letters toward the beginning of the alphabet are richer (shorter measurement), letters toward the end of the alphabet are leaner (longer measurement).
3rd letter indicates starting dimension or root diameter of needle. Letters toward the beginning of the alphabet are richer (thinner diameter), letters toward the end of the alphabet are leaner (thicker diameter).
Needle codes for 28-33mm (90xxx) and
35-41mm (OCxxx) FCRs are listed below.
Code | Taper | L1mm for 28-33mm | L1mm for 35-41mm | Diameter mm |
A | 56.25 | 72.20 | 2.605 | |
B | 56.70 | 72.65 | 2.615 | |
C | 57.15 | 73.10 | 2.625 | |
D | 0d 45' | 57.60 | 73.55 | 2.635 |
E | 1d 00' | 58.05 | 74.00 | 2.645 |
F | 1d 15' | 58.50 | 74.45 | 2.655 |
G | 1d 30' | 58.95 | 74.90 | 2.665 |
H | 1d 45' | 59.40 | 75.35 | 2.675 |
J | 2d 00' | 59.85 | 75.80 | 2.685 |
K | 2d 15' | 60.30 | 76.25 | 2.695 |
L | 2d 30' | 60.76 | 76.70 | 2.705 |
M | 2d 45' | 61.20 | 77.15 | 2.715 |
N | 3d 00' | 61.65 | 77.60 | 2.725 |
P | 62.10 | 78.05 | 2.735 | |
Q | 62.55 | 78.50 | 2.745 | |
R | 63.00 | 78.95 | 2.755 | |
S | 63.45 | 79.40 | 2.765 | |
T | 63.90 | 79.85 | 2.775 | |
U | 64.35 | 80.30 | 2.785 | |
V | 64.80 | 80.75 | 2.795 | |
W | 65.25 | 81.20 | 2.805 | |
X | 65.70 | 81.65 | 2.815 | |
Y | 66.15 | 82.10 | 2.825 | |
Z | 66.60 | 82.55 | 2.835 |
Example 1: A 90FTV needle would have a taper of 1degree 15', an L1 dimension of 63.90mm, a root diameter of 2.795mm, and be intended for use in the small FCRs.
Example 2: An OCEMR needle would have a taper of 1 degree 00', an L1 dimension of 77.15mm, a root diameter of 2.755mm, and be intended for use in the large FCRs.
Needle selection:
Keihin Carburetor Schematics
1st letter: This portion of the needle controls mixture between approximately 1/3 and full throttle. If the engine fails to respond to main jet changes, you may be too lean on this, causing the tip of the needle to be very large. This would tend to artificially limit fuel flow at full throttle, taking control of WOT fuel delivery away from the main jet. Selecting this is much easier than many believe. If you find that mixture is good at 1/4 throttle, but too rich at 3/4, you probably have a needle with too great a taper angle. If the mixture is good at 1/4 throttle, but too lean at 3/4, you probably have a needle with too small a taper angle. I know you went and made sure the main jets were sorted out before testing the needle taper, right?
2nd letter: This generally doesn't need to be played with much. If, when adjusting the clip, you find that you are at the 1st groove and still need to start the taper later, you may need to select a needle with a longer L1 dimension. If you find yourself at the 7th groove and needing to start the taper earlier, you may need to select a needle with a shorter L1 dimension.
Keihin Ks2 Carburetor Manual Pdf
3rd letter: This portion of the needle has the greatest effect on mixture between closed and 1/4 throttle. If the engine is too rich while gradually accelerating through 1/8 throttle, select a needle with a larger root diameter. If the engine is too lean when gradually accelerating through 1/8 throttle, select a needle with a smaller root diameter. You will drive yourself completely batty trying to sort out this if the slow fuel and air jets aren't right. Conversely, you will drive yourself completely batty if you try to sort out the slow fuel and air jets if the needle root diameter isn't right. So you're pretty much screwed either way here. And if you didn't set the float level to 9mm, just go jump off a cliff right now and get it over with because that will have a fairly large effect on how much fuel spurts up through the needle jet when the slide's only open a little bit.
Clip position: This controls mixture between approximately 1/8 to 7/8 throttle. Higher clip position for leaner, lower for richer. Unlike taper, this setting will change mixture (approximately) evenly throughout the throttle position range, with a slight tendency to affect the lesser throttle positions more than greater. You should work to find a needle which allows you to run the clip on the 3rd, 4th (middle), or 5th position. If you find that mixture at 1/3 through 3/4 throttle is too lean, raise the needle!
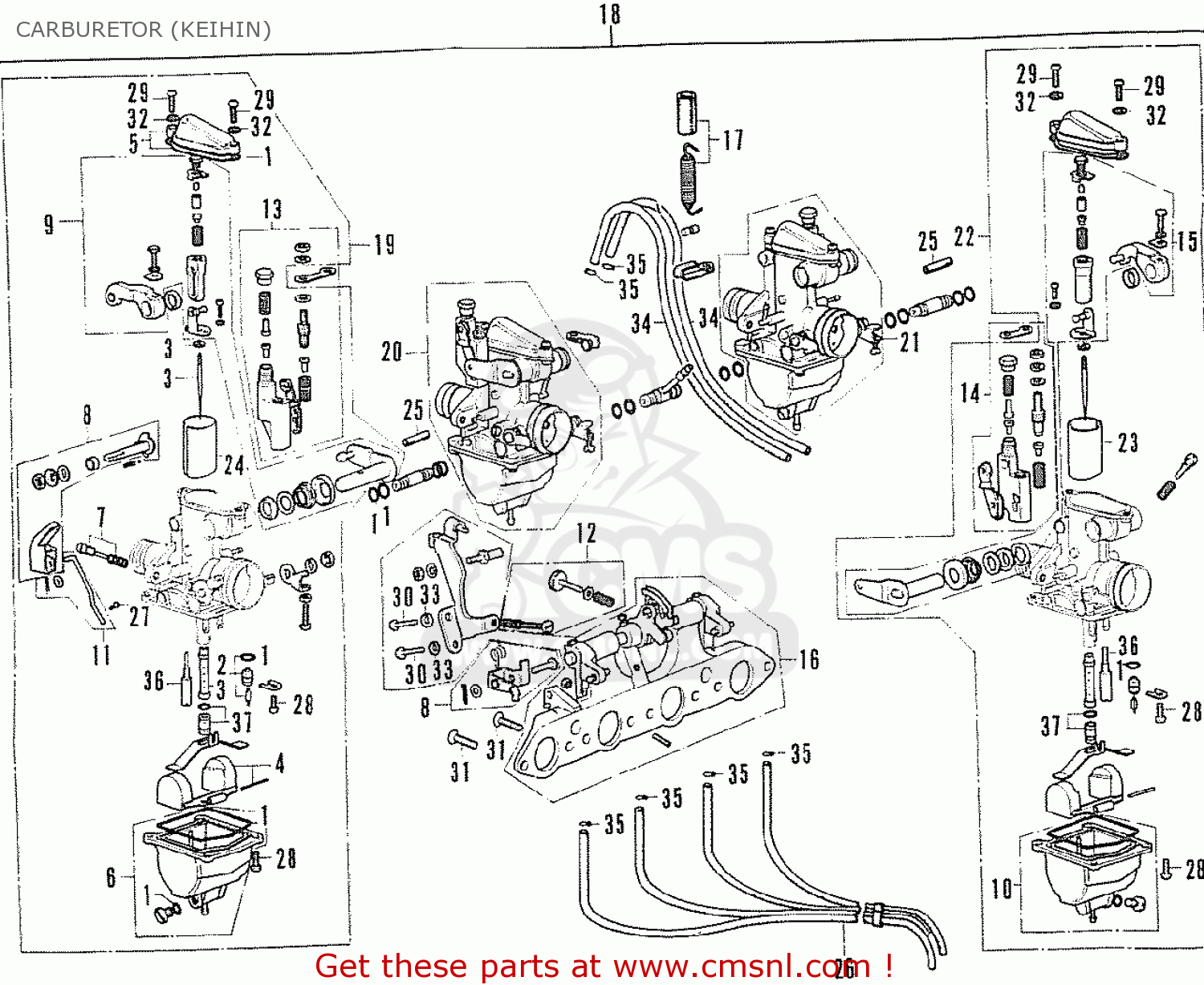
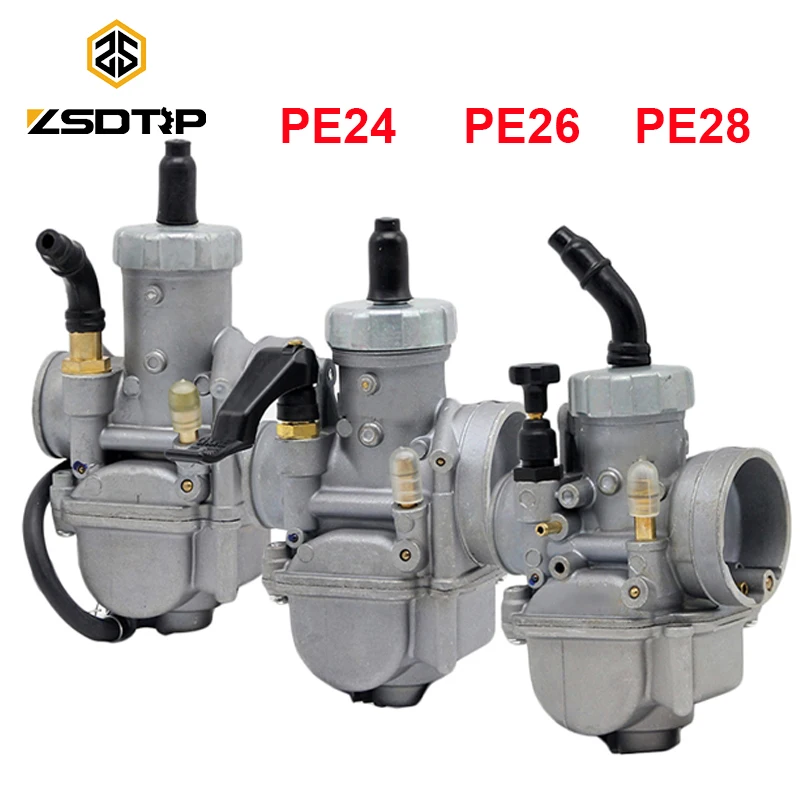
Float level: Higher float levels richen mixture at full throttle low rpm, and part throttle high rpm, lower leans it, but do not change it more than two millimeters in either direction of 9mm. I have caused myself more headaches playing with float level on FCRs than any other adjustment of the carburetor. If you can possibly run the floats at 9mm, do so. To set float level, with the carbs off the bike and the float bowls removed, hold the carbs in such a manner that the float pivots are above the floats. Tilt the carbs until the float you are adjusting just kisses its float valve needle, but doesn't compress the float needle's internal spring. Measure from the float bowl sealing surface to the highest (lowest with the carbs mounted to the bike) point of the float at a 90 degree angle to the sealing surface. Bend the float tab that touches the little nub on the needle to change the float height.
Keihin Carburetors Kohler
Float valve size: These should be sized according to horsepower which will be fed by each carb, and whether the fuel bowls will be supplied via gravity feed or a fuel pump (I suggest using a max pressure of 3.0 psi, since when I tried using 3.5 psi, I kept pumping the cylinders full of gasoline with the engine off...). Do not use 2.8mm or 3.2mm valves with pressure feed, as the increased area of the float valve will allow fuel pressure to overpower the float needle's little internal spring, pushing it down, letting fuel in, and flooding the fuel bowl.
Float valve size | HP per carb | HP per carb |
2.0 | 20-28 | 29-37 |
2.4 | 24-34 | 37-50 |
2.8 | 33-41 | Not recommended |
3.2 | 39-50 | Not recommended |
Cylinder head flow testing
Connecting rod length
How To Identify Keihin Carburetors
Example 1:A 90FTV needle would have a taper of 1degree 15', an L1 dimension of 63.90mm, a root diameter of 2.795mm, and be intended for use in the small FCRs. Example 2: An OCEMR needle would have a taper of 1 degree 00', an L1 dimension of 77.15mm, a root diameter of 2.755mm, and be intended for use in the large FCRs. Needle selection: 1st letter: This portion of the needle controls mixture between approximately 1/3 and full throttle. If the engine fails to respond to main jet changes, you may be too lean on this, causing the tip of the needle to be very large. This would tend to artificially limit fuel flow at full throttle, taking control of WOT fuel delivery away from the main jet. 2nd letter: This generally doesn't need to be played with much. If, when adjusting the clip, you find that you are at the 1st groove and still need to go leaner, you may need to select a needle with a longer L1 dimension. If you find yourself at the 7th groove and needing to go richer, you may need to select a needle with a shorter L1 diminution. This would be the last thing I would change as there is usually another explanation for poor performance. 3rd letter: This portion of the needle has the greatest effect on mixture between closed and 1/4 throttle. If the engine is too rich while gradually accelerating through 1/4 throttle, select a needle with a larger root diameter. If the engine is too lean when gradually accelerating through 1/4 throttle, select a needle with a smaller root diameter. Changing this portion of the needle will move the point of transfer from straight section to tapered section higher or lower on the needle with a richer or leaner straight section respectively. Keep this in mind when diagnosing problems near 1/4 throttle after such a change. Clip position: This controls mixture between approximately 1/8 to 7/8 throttle, with a greater effect on smaller throttle openings. Higher clip position for leaner, lower for richer. You should work to find a needle which allows you to run the clip on the 3rd, 4th (middle), or 5th position. Float level: Higher float levels richen jetting, lower leans it, but I wouldn't mess with it. I have caused myself more headaches playing with float level on FCRs than any other adjustment of the carburetor. To set float level, with the carbs off the bike and the float bowls removed, hold the carbs in such a manner that the float pivots are above the floats. Tilt the carbs until the float you are adjusting just kisses its float valve, but doesn't compress the float valve's internal spring. Measure 9mm from the float bowl sealing surface to the highest (lowest with the carbs mounted to the bike) point of the float at a 90 degree angle to the sealing surface. Bend the float tab to correct. Once this is set on each carb, reassemble the carbs and mount them to the bike. Connect the fuel line and apply the fuel pressure the carbs will see during operation be it gravity feed from the tank or pressure feed from a pump. Use a sighting instrument connected to the float bowl drain to view the fuel level within the float bowl on each carb. Record levels. Any major anomalies warrant investigation into float buoyancy and needle valve/seat condition. Small differences (one or two millimeters) should be corrected by readjusting the float level on the affected carb. Float valve size: These should be sized according to horsepower which will be fed by each carb, and whether the fuel bowls will be supplied via gravity feed or a fuel pump (3psi suggested). Do not use 2.8mm or 3.2mm valves with pressure feed, as the increased area of the float valve will allow fuel pressure to overpower the float's buoyancy, flooding the fuel bowl.
|